The 'Eco-Friendly' Promise: Why PLA Biodegradability Confuses So Many Makers
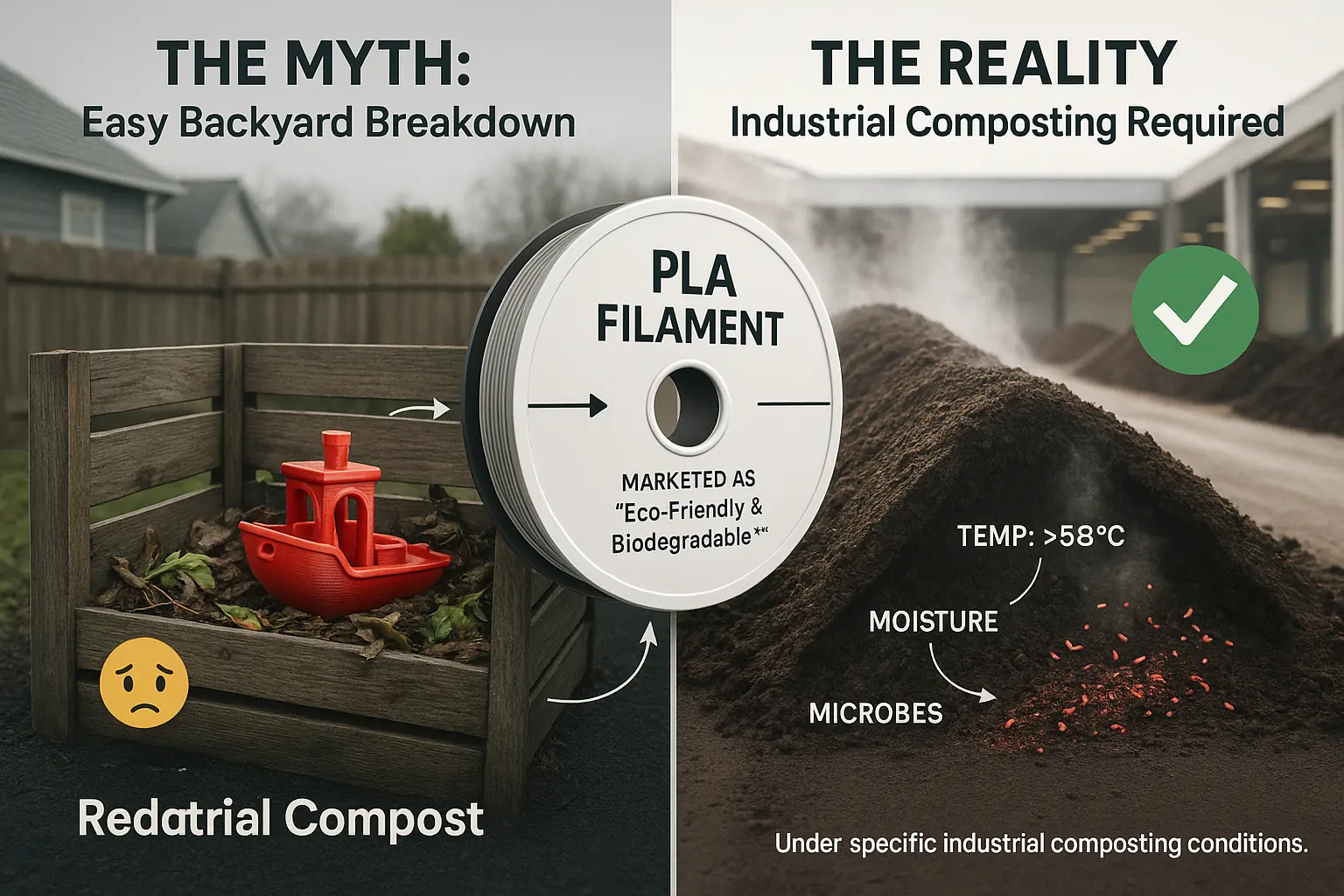
Many makers grab that shiny new PLA spool. They feel good about its 'eco-friendly' label. But what does 'biodegradable' truly mean for your failed prints? Marketing often paints a simple picture. This picture frequently misleads. User misconceptions about PLA are widespread. Our UGC analysis reveals this common frustration. We are here. To clarify.
Here's the kicker. That 'compostable' PLA label often hides a huge catch. Your backyard compost pile? Probably not enough. Many makers discover this reality. The hard way. Our deep dive into maker forums confirms widespread disappointment when PLA prints remain stubbornly intact. Scientific papers echo these user experiences, highlighting that PLA often needs specific industrial composting conditions to truly break down.
So, let's cut through the greenwashing together. This page tackles PLA's end-of-life mystery. We use hard science. We use countless maker experiences. These experiences are hard-won by individuals attempting to go green. You will find clear, actionable insights here. No more confusion. Just facts.
PLA & Home Composting: Why Your Backyard Isn't a Biodegradation Wonderland
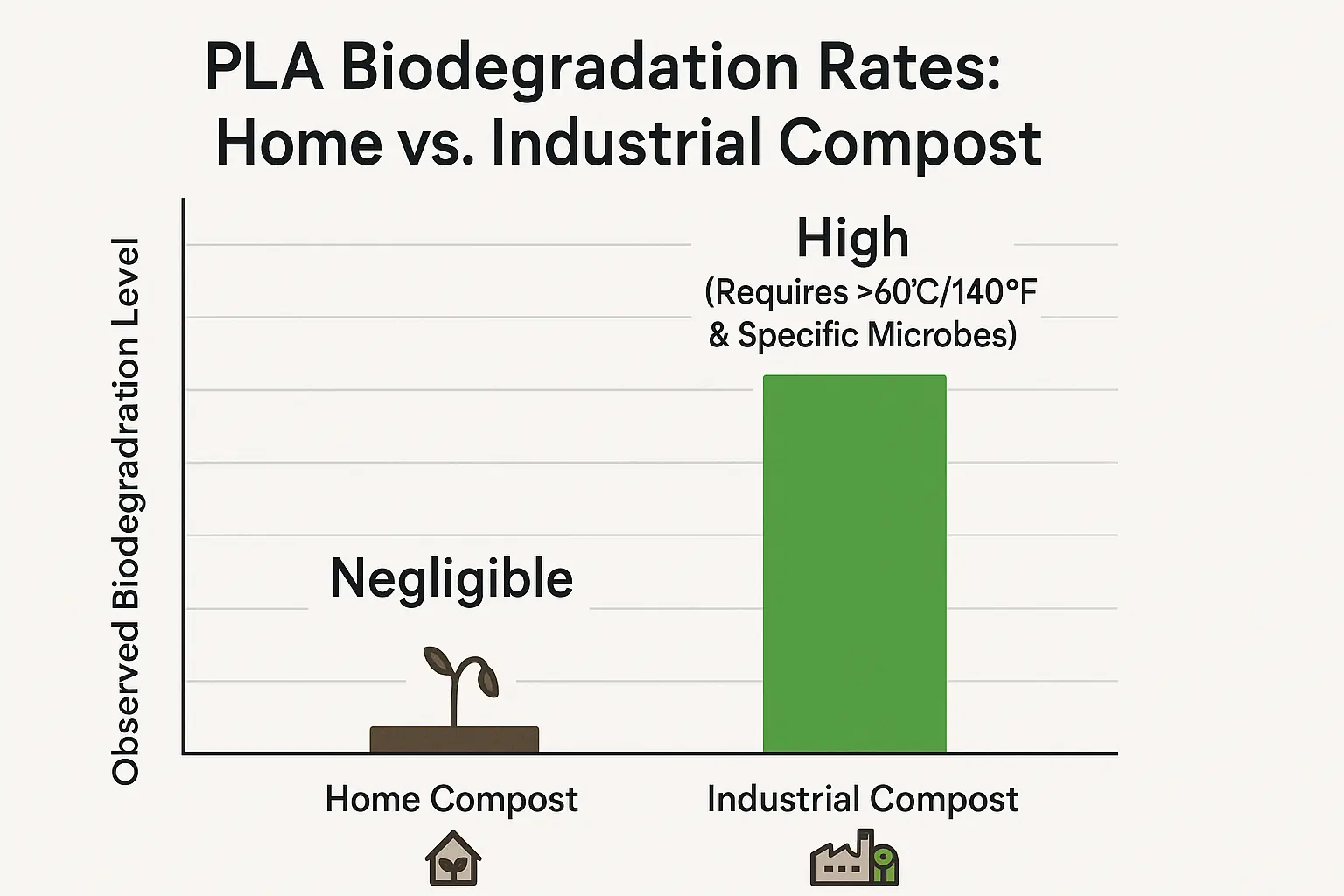
Let's be blunt: that 'compostable' label on your PLA spool often misleads. It rarely means your backyard compost pile can handle it. Our analysis of extensive maker discussions reveals a clear pattern. Attempts at home composting PLA almost universally end in disappointment. Why this consistent failure? Home composts lack sufficient, sustained heat. They also lack the specific microbial populations PLA requires for breakdown.
For PLA to truly biodegrade, it demands the specific, controlled conditions of industrial composting facilities. These operations maintain sustained high temperatures. We're talking over 140°F (60°C) for extended periods. High humidity and a precise, managed mix of microorganisms are also absolutely essential. Your average backyard heap simply cannot achieve or maintain these rigorous parameters. This is a critical, often unspoken truth. Manufacturers frequently omit this vital context from product information.
We've reviewed countless stories from the maker community. Makers diligently bury their failed PLA prints, hoping for natural decay. Months, sometimes a year later, they unearth them. The prints often look remarkably unchanged. One user shared finding a "perfectly preserved Yoda head after a full year in the compost bin!" This experience, echoed by many, highlights the real-world frustration. It also shows a significant information gap regarding PLA's actual end-of-life requirements.
When you see 'compostable' certifications like ASTM D6400 or EN 13432 on PLA packaging, understand their meaning. These standards certify PLA for those demanding industrial composting conditions. They do not apply to your home garden setup. This is a crucial technical distinction. It is often lost in marketing translation, yet it's vital for understanding where your used PLA truly belongs for proper disposal.
Even if PLA seems to break into smaller pieces in a home compost, true biodegradation is unlikely. It often just fragments. This process creates microplastics. These tiny plastic particles then persist in the environment. This introduces a different, yet still significant, ecological concern. Not true composting.
PLA Disposal Reality Check: Where Does Your Filament Truly Belong?
PLA Disposal Reality Check: Where Does Your Filament Truly Belong?
Answer a quick question to understand the most likely fate of your PLA prints:
So, what did your local reality check reveal? PLA disposal options truly hinge on your local waste management systems. Many makers find PLA is often landfill-bound, despite hopeful marketing claims. Access to industrial composting facilities remains limited for individual users. Knowing your local infrastructure is vital.
But don't despair! You still hold power, even if industrial composting isn't an option. Consider optimizing your prints meticulously; this directly cuts down on material waste. Many online communities discuss local PLA collection points or recycling initiatives run by fellow makers. The most sustainable print? Often, it's the one designed well enough to avoid the bin entirely. What successes or challenges have you encountered with PLA disposal in your area?
Beyond PLA: What About PETG, PHA, and the Microplastic Shadow?
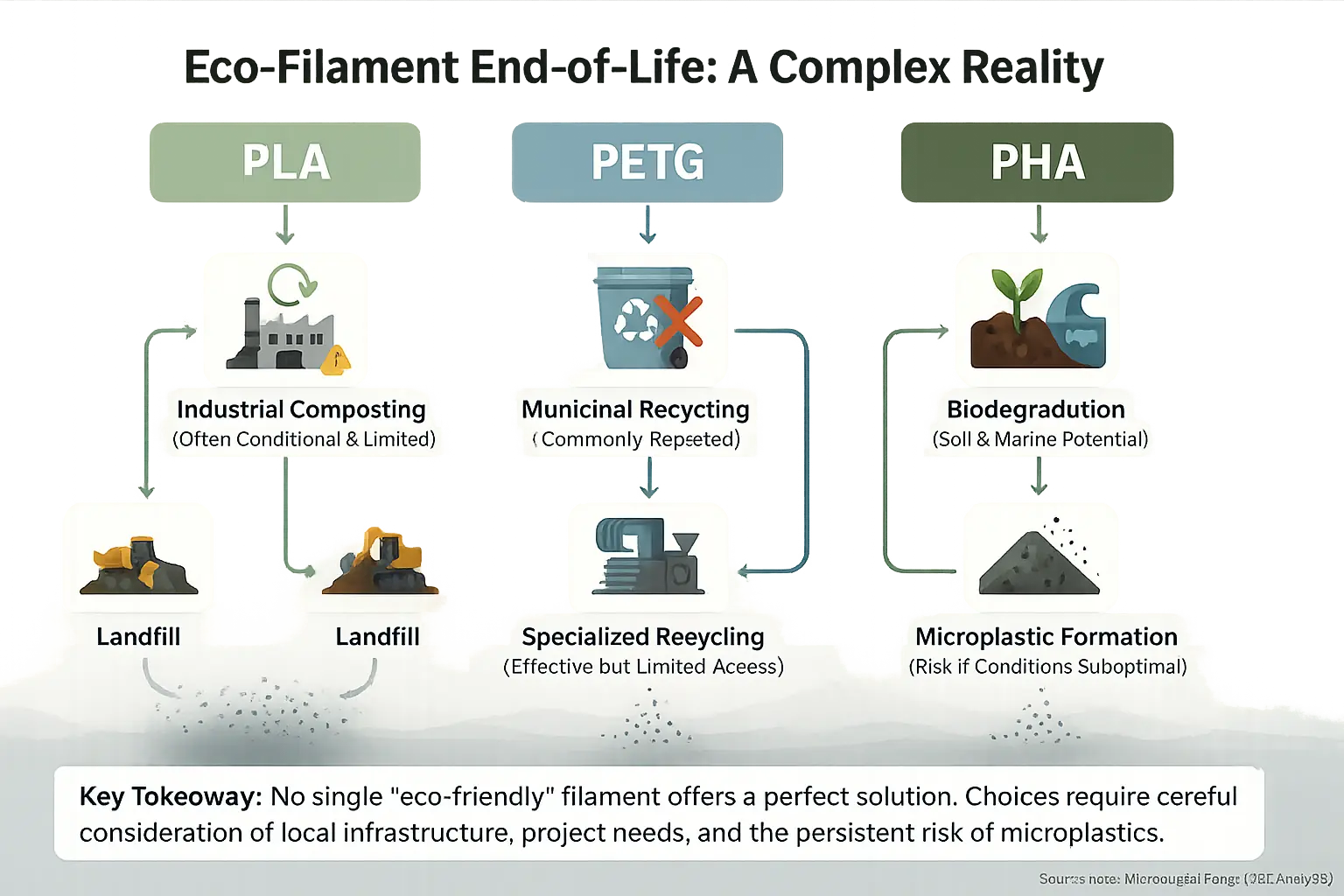
PLA's biodegradability presents challenges. What about other "eco-friendly" filaments? Makers often consider PETG. Companies promote PETG as recyclable. This claim is technically true. The practical reality for makers proves far more complex than simple curbside bin disposal.
Maker discussions reveal common PETG recycling frustrations. PETG is recyclable. Yet, local facilities often reject 3D printed PETG. Contamination concerns and differing melt characteristics are primary reasons. Municipal systems lack infrastructure for diverse 3D print waste shapes. Many makers see their "recyclable" PETG tragically head to landfills. This situation highlights a significant gap: technical recyclability versus practical hobbyist options. Specialized services can recycle PETG effectively, but their accessibility varies considerably.
PHA filament emerges as another option. Polyhydroxyalkanoates offer truly promising bioplastic properties. PHA biodegrades in diverse environments. This includes soil and even marine conditions. The current reality? PHA remains less common. It is often more expensive than PLA or PETG for hobbyists. Real-world user experiences with PHA are still developing, though a dedicated community shares printing insights. Moisture sensitivity can challenge PHA printing if not managed carefully by users.
Microplastics. The hidden issue. Even "biodegradable" plastics present this risk. Improper conditions prevent full decomposition. These plastics can fragment into tiny particles. Microplastics create distinct environmental hazards. Marketing materials frequently omit this critical detail. Makers must understand this unspoken truth for informed choices.
Choosing eco-filaments involves complex trade-offs. No single perfect solution exists. The "best" filament often depends on local recycling infrastructure. Project needs also heavily influence material selection. Makers in online communities consistently highlight these nuanced realities. Understanding these factors empowers genuinely responsible creation.
Beyond the Bin: Responsible Disposal & The Bigger Picture for Makers

So, what is the ultimate takeaway from this deep dive into 'eco-filament' end-of-life? The most sustainable filament often needs no disposal. This insight means focusing fiercely on waste reduction at its source. Optimize print settings to minimize failures, design parts for durability, and choose materials wisely from the start.
Waste is sometimes unavoidable. Always think 'upcycle' before 'recycle' or 'dispose.' Our community is a goldmine of ingenious ideas. Failed prints become new, useful objects – from artistic mosaics to practical organizers. Exploring local maker groups for collective recycling initiatives or material swaps also unlocks new possibilities beyond your curbside bin.
MicroSustain Forge's goal is not just debunking myths. It is arming you with practical, honest insights. These insights help you make genuinely sustainable choices in your workshop. We will keep digging into 'unspoken truths' and sharing the collective wisdom of makers, because together, we can forge a more sustainable future for micro-manufacturing.